Project Management
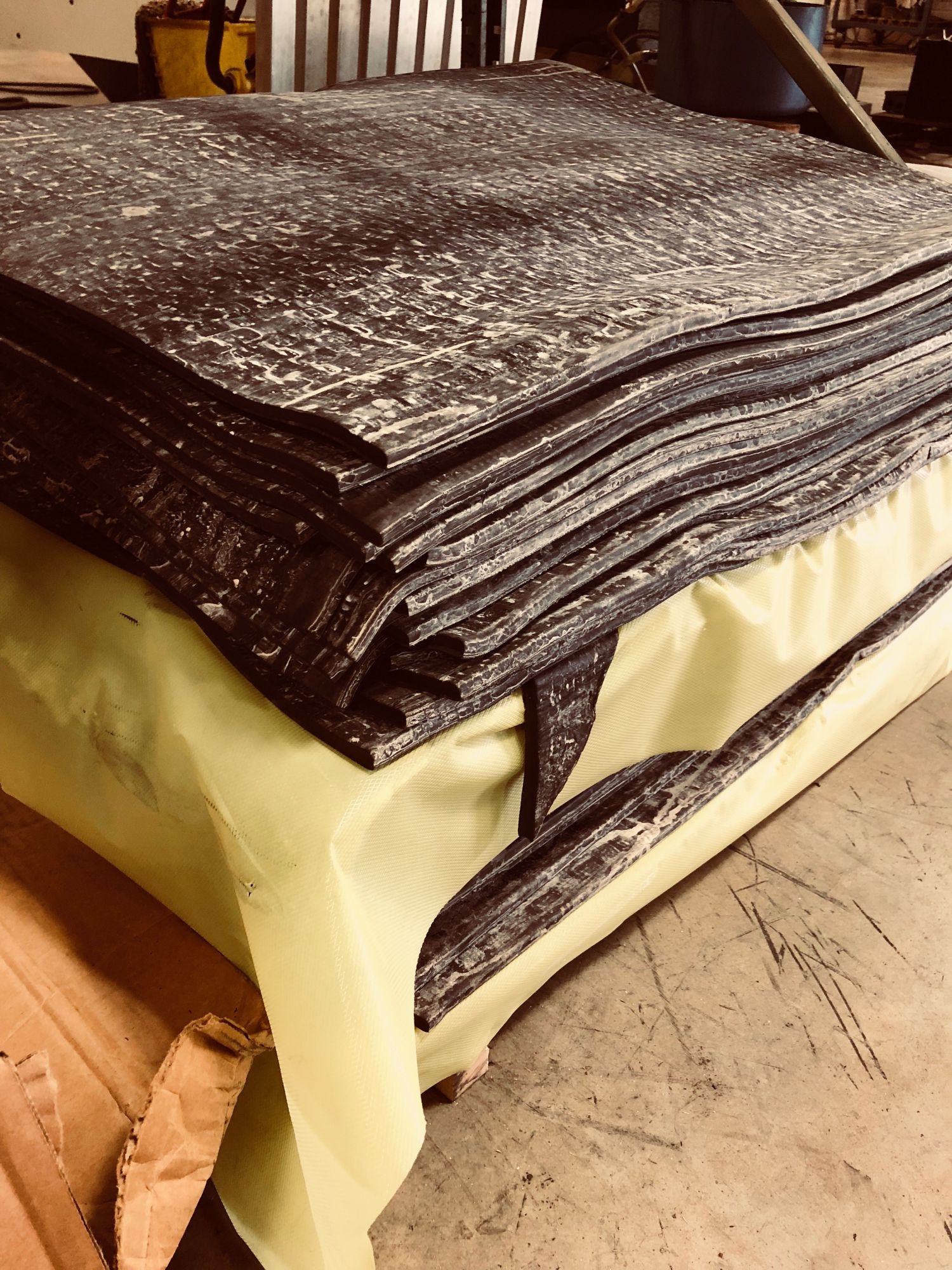
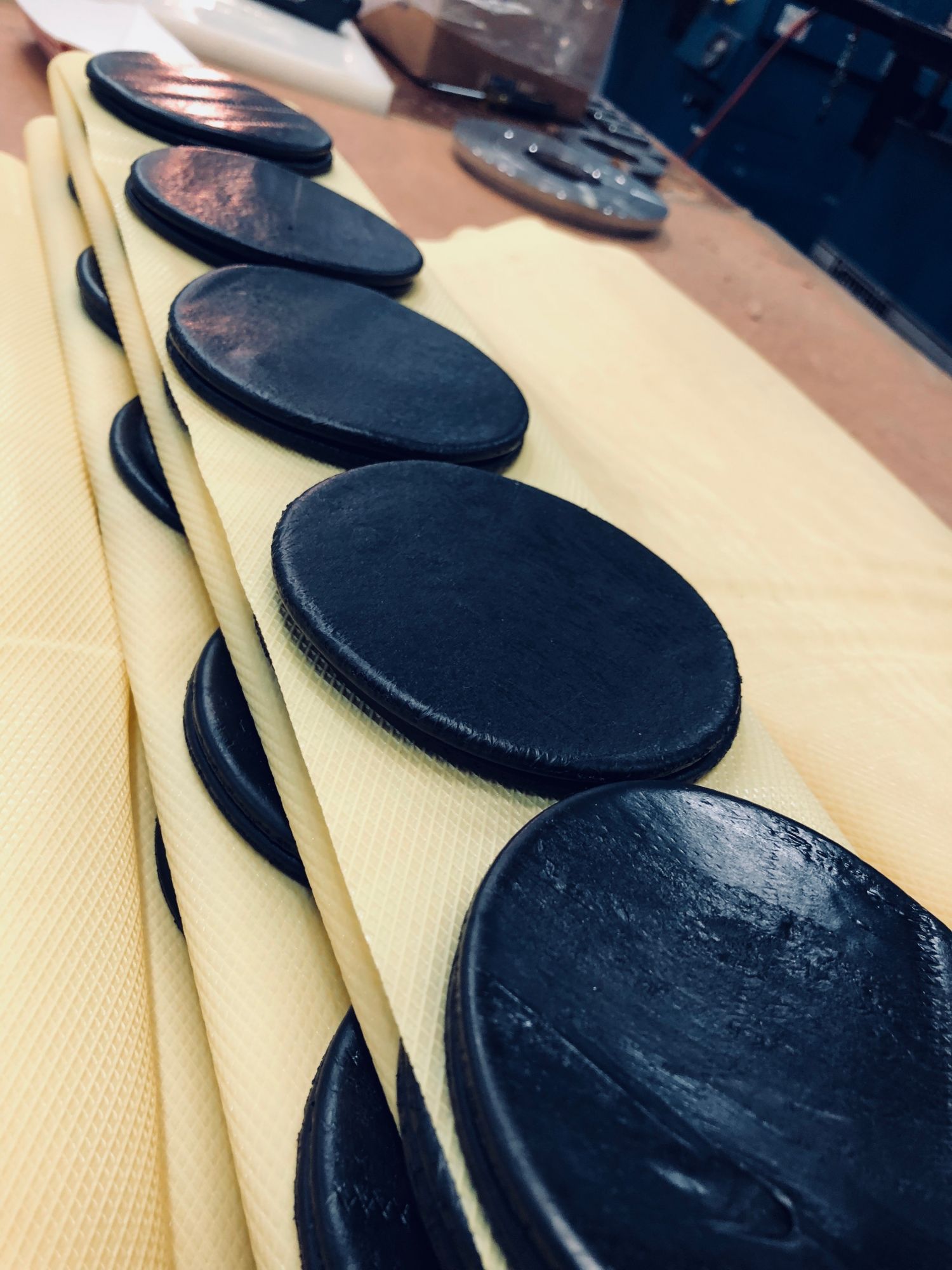
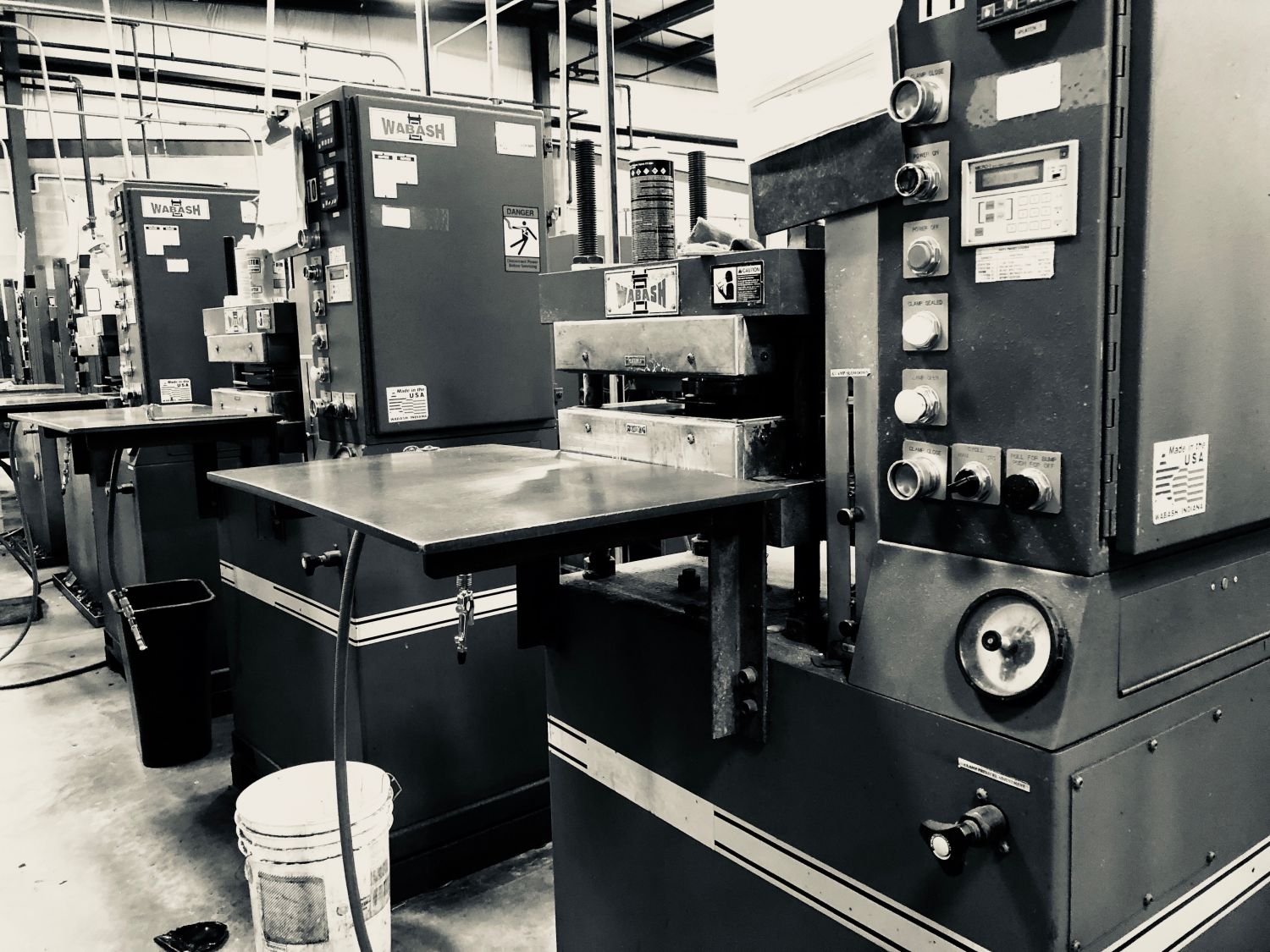
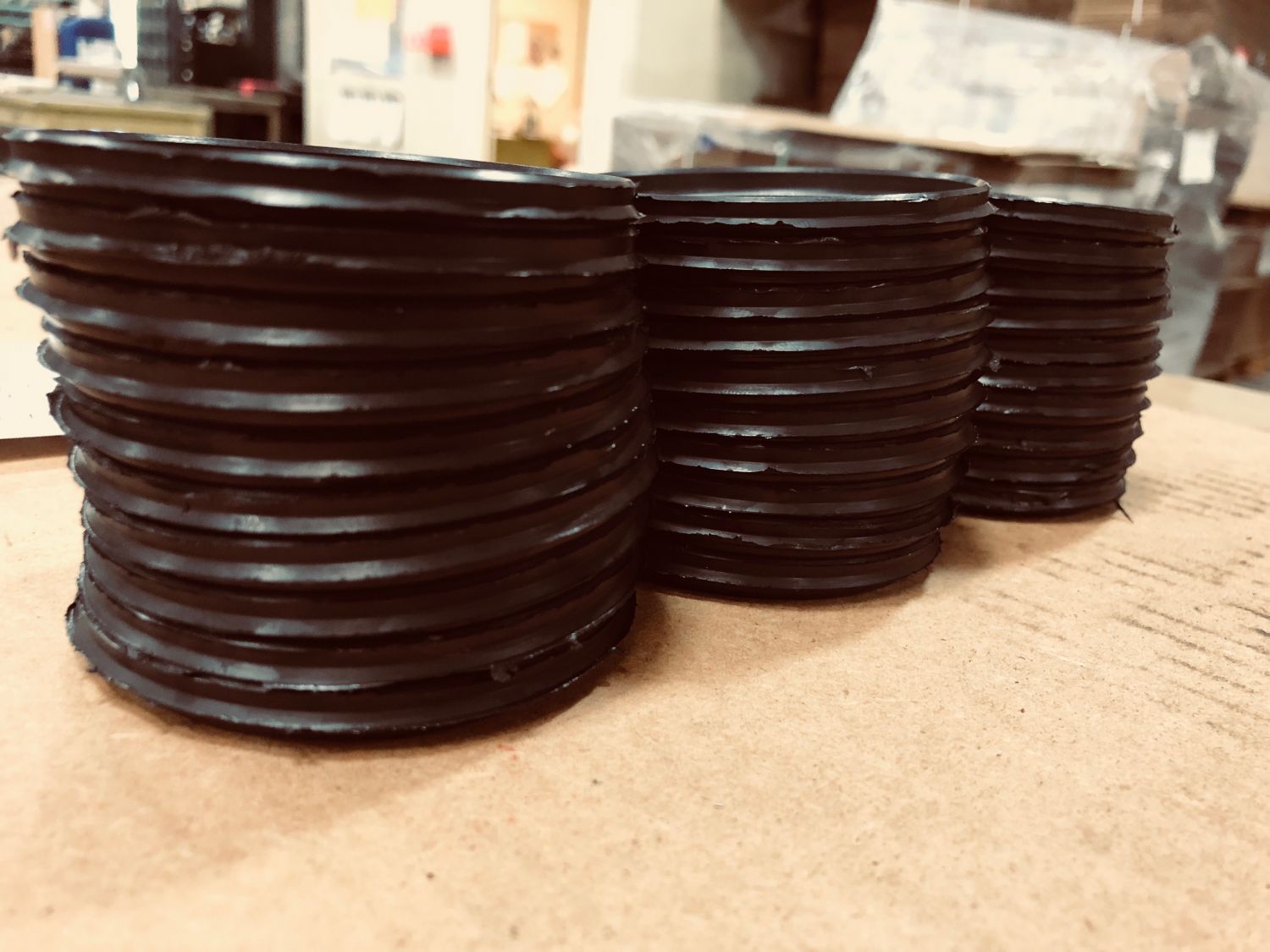




Our processes are constantly evolving to maximize our efficiency and improve our service. It starts with our Sales team, or sometimes even our President, Michael J. Myhal, Jr. himself, as your initial contact. Working closely with you, we will help you choose the right elastomer for your project. With the help of our production and quality team we can then plan out the best molding processes to help you be both cost effective and time efficient. We’ll submit a proposal with several options, and will follow up with a contract review to make sure everything is to your liking.
Once your project hits the shop floor, our ISO Certification ensures that best practices are followed every step of the way. Your parts are inspected throughout each step of the production process to make sure you are getting the absolute best quality parts.
Because our entire team, even our company President, is available to customers 24/7, you’ll never have to wonder how your project is progressing.
We encourage open dialogue between our customers and our project management team. We want to make sure your experience with TMI is as efficient and hassle-free for you as possible. In fact, it’s just as important to us as all the expertise and technology involved.
Our Team
Phone: 330-270-9780
Fax: 330-270-9845
info@teamtmi.com
Patricia Odell, Scheduling/Customer Service
Patricia is not only our Scheduling, Customer Service and Quality Control guru, she’s also the very first employee we hired, back in 1984. That’s a LOT of dedication. But that doesn’t mean she doesn’t have an amazing life outside of work. She lives on land that has been in her family for 65 years, in a log home that she and her husband actually built themselves nearly 30 years ago. Her yard boasts around 30,000 daffodils she’s been dedicated to for years, and she’s been to 37 of our country’s 50 states so far. If you happen to meet her, get on her good side: she’s known for her chocolate chip cookies and just may share some.
Dean Ciccone, Plant Manager
Not only does Dean share the same last name as the Material Girl, Madonna, he’s been with TMI since that singer was just getting her start over 25 years ago. When he’s not managing the day-to-day operations here, you can find him spending time with his wife and four kids, golfing, cooking or even making his own wine. Oh, little known fact: Dean used to be a pole-vaulter when he was younger. Ask him about it.
Gary Blockinger, Quality Coordinator
Gary doesn’t just know a thing or two about quality, he practically invented it. Really. When he worked for Paragon Industries, he actually helped develop the QS9000 quality standard for the “Big Three” US automakers and was responsible for its training requirements. Before that he spent 31 years working in the Quality department for Delphi, a major supplier to GM. He also spent four years in the US Navy, complete with a Top Secret clearance and an Honorable Discharge. He values quality in his family life, too. He’s been married for 45 years, has three daughters and seven grandchildren, loves the outdoors and is dedicated to exercising to stay healthy and fit.
Shayn Danks, Sales & Business Development
Finding new ways to improve our customer relations and grow our customer base is vital to the longevity of our business. That’s where Shayn comes in. Whether its updating our website to be more customer friendly or communicating with current or potential customers, Shayn will work to make your experience with TMI better. His time away from TMI is spent with his wife, volunteering at their church, working out, and watching Cleveland sports!